Ball valves for pharmaceutical applications
Valves for pharmaceutical applications
For applications in the field of mixing, clean steam and transport of valuable Active Pharmaceutical Ingredients (APIs), we have various valves that ensure that contamination cannot take place. Within these processes some aspects are crucial, such as avoiding dead spaces, surface treatment and the use of contamination-avoiding materials. In addition, we have PTFE expansion joints and PTFE-coated pipe components that ensure that the supply of chemicals takes place safely without the risk of corrosion.
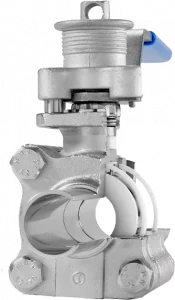
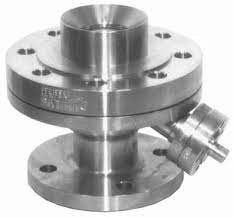
Mixing APIs
Our bottom valves are used in tanks, filter dryers and reactors mixing APIs, among others. These bottom valves can be mounted directly into and onto the tank, dryer or reactor by custom flange connections. To prevent rouging and degradation of materials, only low carbon alloys (316L) or exotic materials such as Hastelloy C22 are used. In addition, these bottom taps are fully cleanable between production batches and minimize dead spaces.
Transporting APIs and clean steam
Our Habonim sanitary ball valves are used in clean steam processes and for conveying APIs. In these applications, a high purity, or sanitary design (ASME BPE) is required with a tube bore passage. Also, in some cases these ball valves need to be Fire Safe (API 607) and ATEX certified combined with the demand for food grade approvals (USP VI / FDA / EN 1935). Habonim sanitary ball valves meet this complex demand.
We supply a wide range of sanitary ball valves for different process conditions. Please contact our specialists for customized advice.
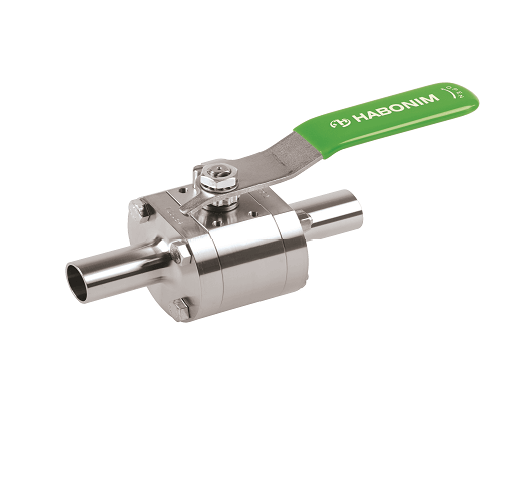
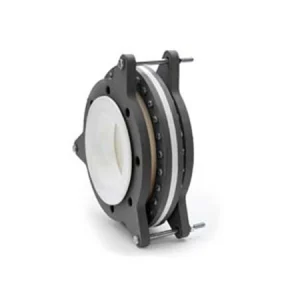
The transportation of chemicals
Many pharmaceutical production processes require the supply of various chemicals that need to be stored and transported in a vellified manner. Our PTFE expansion joints, PTFE-coated valves and PTFE-coated pipe parts guarantee this safety by preventing corrosion of steel parts. We provide customized components to always guarantee a suitable solution.
Custom valves for pharmaceutical applications
Within pharmaceutical processes, traditional, proven solutions are often relied upon to monitor process assurance and integrity. In some cases, this leads to the maintenance of old, dated valve designs. When the unique manufacturer of such a dated design ceases to exist or decides to phase out the design, this can lead to a loss of availability and major risks to process continuity. Hanwel provides one-to-one replacements of special valve designs that are discontinued or limited in availability. We do this through a process of reverse engineering in which we develop and deliver a suitable replacement of the current design in cooperation with the customer. This ensures the continuity of production processes at all times.
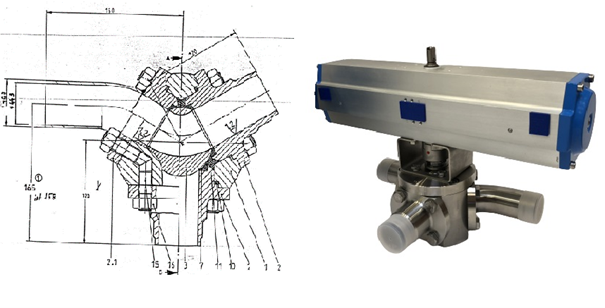