Trunnion mounted ball valves vs. floating ball valves
What are the exact differences between a floating ball design and a trunnion ball design?
The main difference between the two designs is that a trunnion ball is attached to both the top and bottom by a shaft while a floating ball is only attached to the top by the shaft. Thus, in a floating ball design, the ball ''floats'' in the seats.
In a floating ball design, the ball is pressed against the downstream seat by the in-line pressure creating the seal. When the valve is operated, the ball must be rotated against both the line pressure (∆p) and the seat pressure toward the open position. This leads to a high torque requirement as the dimensions and/or pressure rating increase. As a result, floating ball valves become more difficult to operate as they become larger, as the pressure class increases and/or as the seat becomes more robust. The latter case occurs when a metal seal is used.
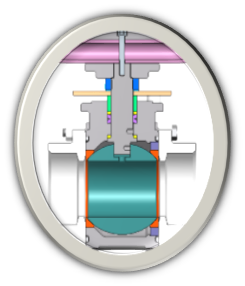
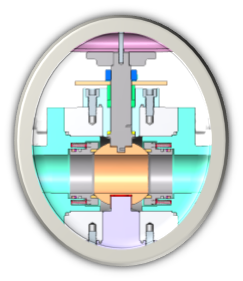
In a trunnion ball valve, the ball is attached at the bottom to a central shaft -the trunnion- which fixes the ball between the shaft and the trunnion. In other words, the ball does not swivel. The seats are pressed against the ball by the pressure of the medium, creating the seal. Thus, during actuation, the ball does not have to be actuated against the pressure of the line (∆p) but only against the pressure of the seats.
As a result of these differences, the required tightening torque of a trunnion ball valve is lower than that of an equivalent floating ball valve. In other words, a DN200 metal-seated floating ball ball valve requires a much larger actuator than a DN200 equivalent trunnion ball valve, so the overall cost of the package may be lower for the trunnion design. Also, the trunnion design demands less from a seat, making the design as a whole more stable under extreme conditions.
This makes the trunnion ball valve more robust and better suited to high and fluctuating pressures and large dimensions than the floating ball. Another advantage of the trunnion over the floating design is the fact that a trunnion is often fitted with a drain or bleed connection, allowing the valve to be used as a dual safe device. Finally, a trunnion ball valve automatically acts as a relief valve as soon as the pressure in the central cavity exceeds the spring force of the seats. In this case, the seat springs are relieved and the excess pressure is sent back into the pipeline. Because of the above reasons, trunnion ball valves are commonly used in the offshore industry and oil & gas.
A disadvantage of the trunnion ball valve compared to the floating ball is obviously represented by the significantly higher cost associated with the design. As a result, the floating ball design is more widely used than the trunnion design.
Our specialists will be happy to give you non-binding advice on this consideration so that you apply the right design at all times.
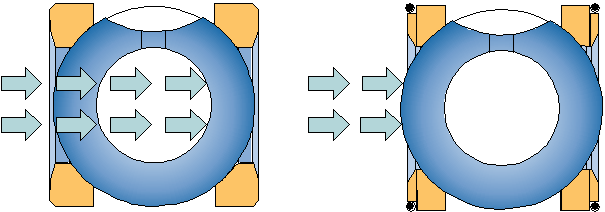