Stock management during running stop
The challenge
A major client in the petrochemical industry was preparing for a long-term project to combat contact corrosion on piping systems and in the underlying structures. That this long-term project would require a large number of pipe supports was clear. However, it was unknown at what point what demand would arise. It was essential for the continuity of the project and its schedule that a continuous flow of products be available. Drying up the flow of products would result in project downtime.
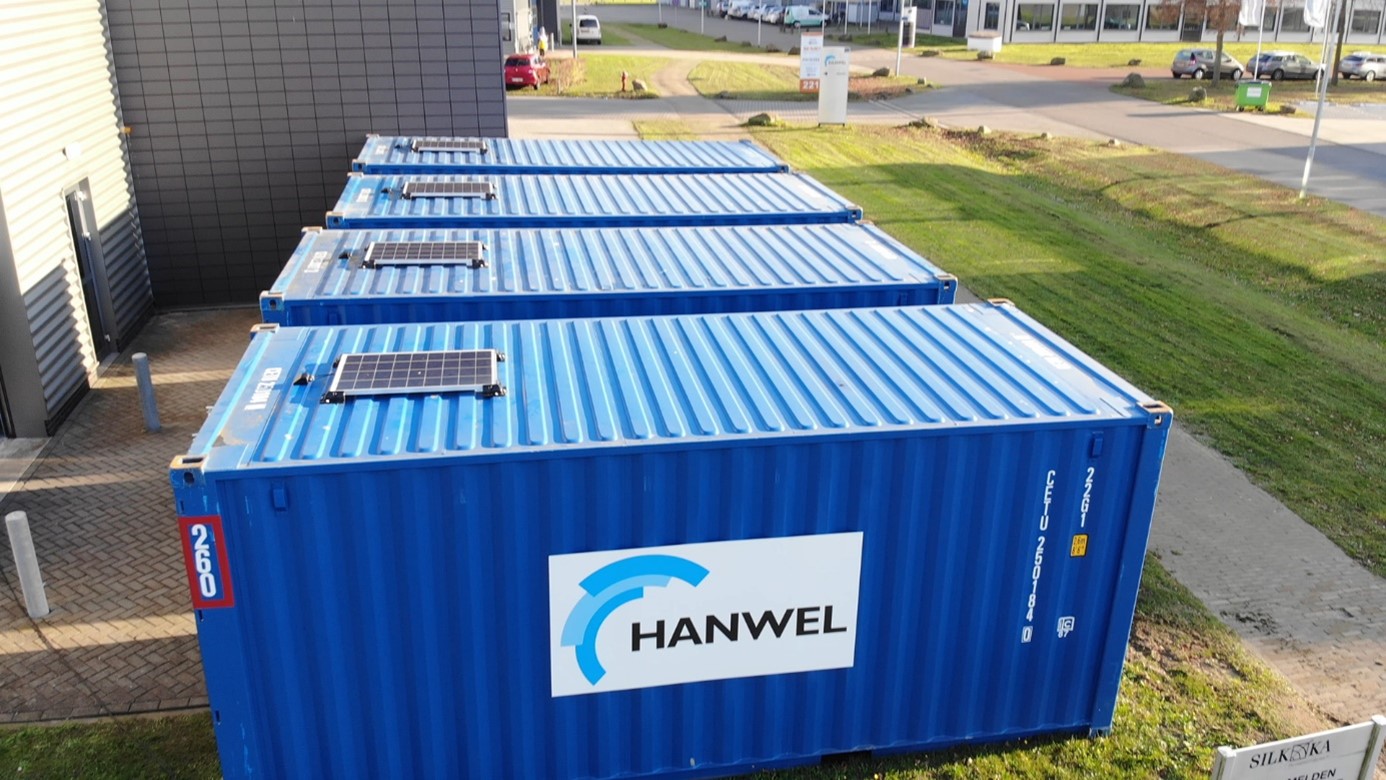
How did Hanwel help?
The challenge in this was twofold: on the one hand, a continuous flow of products had to be made possible. On the other hand, we had to be able to be flexible and either squeeze or significantly increase the flow if the short-term schedule required it. To meet this demand, Hanwel developed a completely self-contained and utility-free warehouse and delivered it on site.
The warehouse consists of four containers and is completely self-sufficient in terms of light, electricity and fixtures. The layout was determined in consultation with the customer.
To keep track of the outgoing products, a digital checkout system is built in, which scans the products as soon as they leave the container. This scan is read out periodically by Hanwel in order to keep track of usage and replenish the stock when the predetermined lower limit is approached.
The result
With the warehouse on site, the customer has access to the required components at all times. The stock is controlled and maintained by Hanwel B.V., so the customer is completely relieved. The result is full continuity of the project and no downtime because components are out of stock. This allows the customer to fully focus on its core business: the successful execution of the planned work.
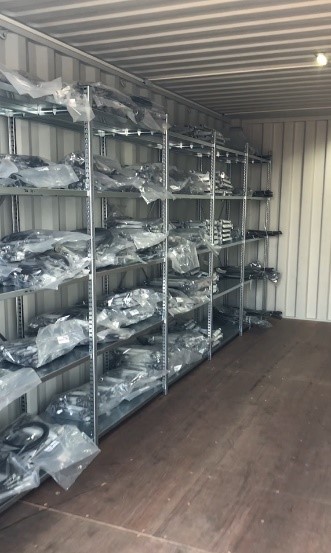